R&D activities for social good
- #social good
- #fairwood
sustainability
Hand Design
R&D activities aimed at realizing social good
Using our own hands to bring out the new charm of wood
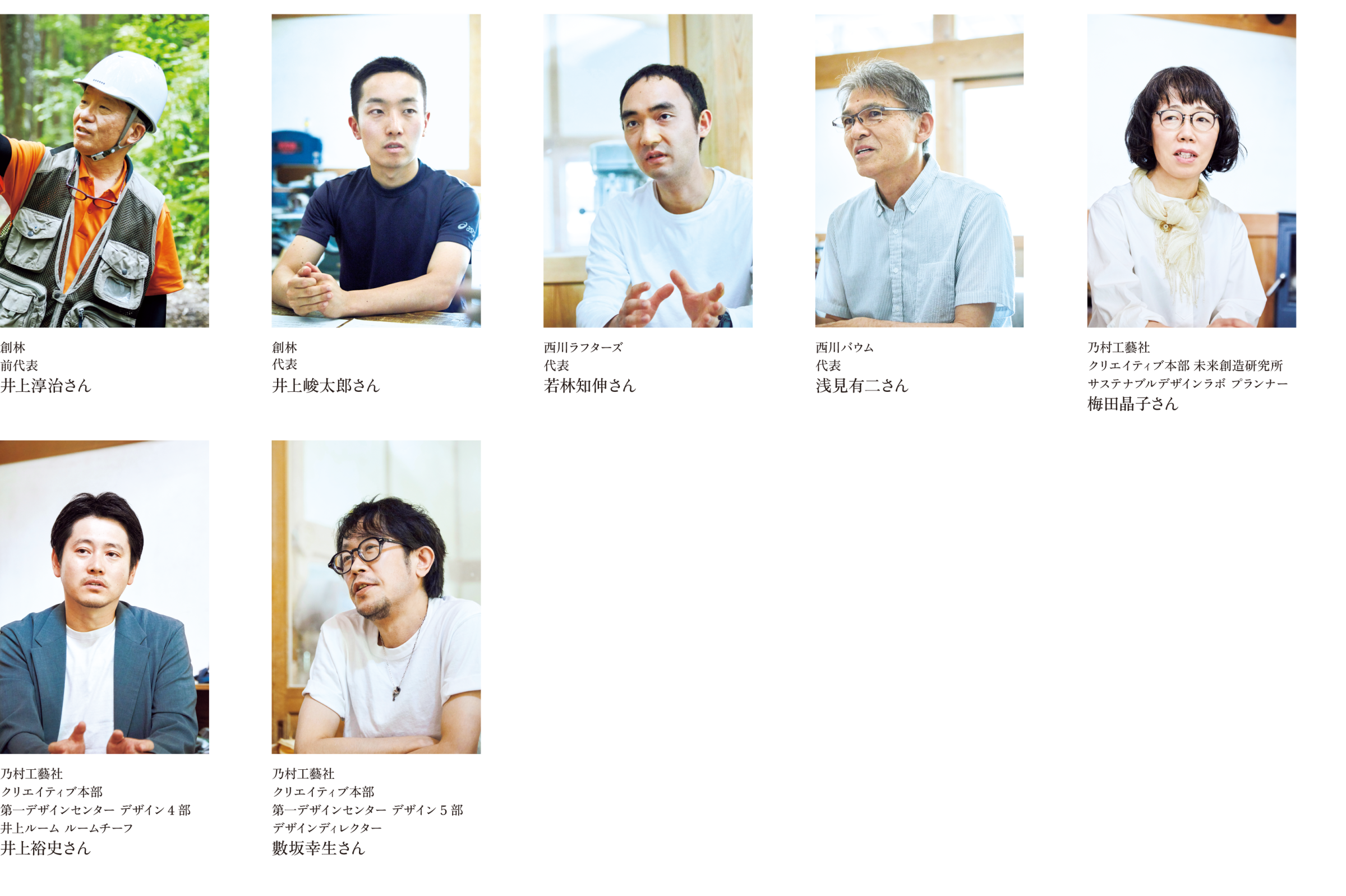
We want to protect Japan's forests - everyone wants to do this, but when it comes to how to achieve it, it's hard to find an answer. However, there is a team that thinks together with the people in timber-producing areas and keeps working to inject new value into their work.
The culture of using wood has disappeared somewhere.
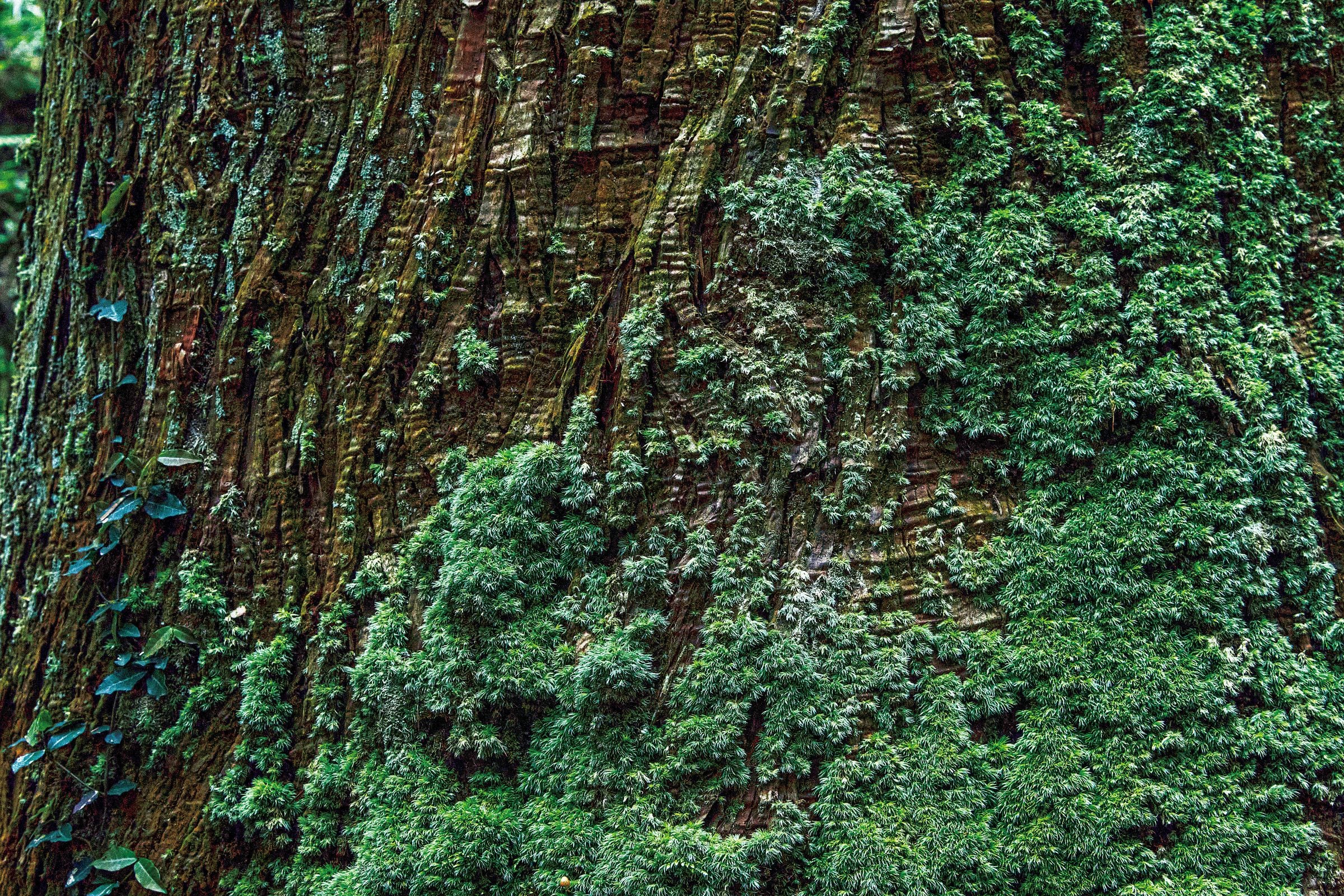
Hanno City, Saitama Prefecture. This area has long been known as a land of thriving forestry. Junji Inoue, former representative of Sorin-shin, a local company that has been engaged in forestry for generations, is the head of the family in the 10th generation.
"In the Edo period, felled timber was built into rafts and transported along the river to lumber yards in Senju or Fukagawa. The timber was called Nishikawa timber because it was transported by river from the west, and the name Nishikawa timber can still be found in documents from the Genroku period."
Nishikawa lumber reached the center of Edo, and became the main source of lumber for the city. Due to the high quality of the wood, forestry quickly became an established industry.
"There is even a story that Hanno became prosperous whenever there was a major fire in Edo. Nowadays, the main trees are cedar and cypress, but in the past there were also sawara and pine trees. The trees in this area grow relatively slowly, so the annual rings are fine and the wood is dense and of high quality,, hard. However, because it is so hard, it has the disadvantage of being prone to cracking.
So, artificial planting began in the middle of the Edo period, and forests were created in a planned manner. At that time in various parts of Japan, forestry was still mostly just cutting down trees," says Inoue.
Forestry involves planting seedlings, caring for and managing the forest over the long term, and then harvesting and shipping the trees in a cycle of about 30 to 60 years. This cycle has continued uninterrupted since the Edo period, but something strange happened during the postwar period of rapid economic growth.
According to statistics from the Forestry Agency, domestic timber shipments peaked in the early 1950s, with the domestic self-sufficiency rate exceeding 90%. Since then, although overall demand for timber has grown, domestic timber shipments have plummeted due to pressure from imported timber. By around 2000, shipments had fallen to one-third of their peak, and the self-sufficiency rate had fallen to 18.8% (2002). Currently, the situation is recovering, but shipments are still only about half of what they were at their peak.
In many parts of Japan, trees that have reached the age of harvesting are left with nowhere to go. Why has the demand for domestic timber fallen so far? Shuntaro Inoue, who took over from his father and is now the representative of Sorin, cites the fact that trees have become less important in people's lives.
"Wooden products have become less familiar to us. Because they are not so familiar to us, many people don't even know the difference between wood species, such as cedar and cypress. What's more, they don't even stop to think about how they get to their hands. The value of wood, and the value of mountains and forests, is not being conveyed."
Wakabayashi Tomonobu, representative of Nishikawa Rafters, who studied at the same forestry vocational school as Shuntaro and started his own company to spread awareness of the value of forests, says there has been a big change in lifestyle.
"I think the biggest change is in lifestyle. Even in housing construction, we have moved away from solid walls with exposed pillars and beams to large walls that cover the pillars and beams with plasterboard and wallpaper. There are also very few furniture items such as tables and chairs made from solid wood."
Asami Yuji, president of Nishikawa Baum, who established a wooden product planning company with the aim of incorporating wood into modern people's lives in new ways, continues:
"It seems that the culture of using wood was lost somewhere along the line. In my grandfather's generation, there were many wooden household items, and solid wood was also used quite a bit. People back then knew how to use and maintain wood.
However, after the period of rapid economic growth, new materials such as plastic came into use, and even wooden furniture began to be sold with a urethane coating to prevent scratches. We entered a culture of disposable, cheap, "smooth and shiny" items. At that time, people in the wood industry did not propose products that properly promoted the value of wood, and instead leaned toward "smooth and shiny" products, which I think was a mistake, and I think that's what I regret, including my own reflection on this."
After working for a long time with wood products, Mr. Asami is now aiming to distribute wood in a way that is different from traditional building materials, etc. Forestry is supposed to be sustainable in a long-term cycle, but unless the uses are expanded and a balance is struck between production and consumption, it will not circulate.
While these feelings are held by the producers, there has also been a change in awareness among those who use the wood, and little by little cooperation between the two parties is beginning to take shape.
It's important to visit the place where it's produced, even just once.
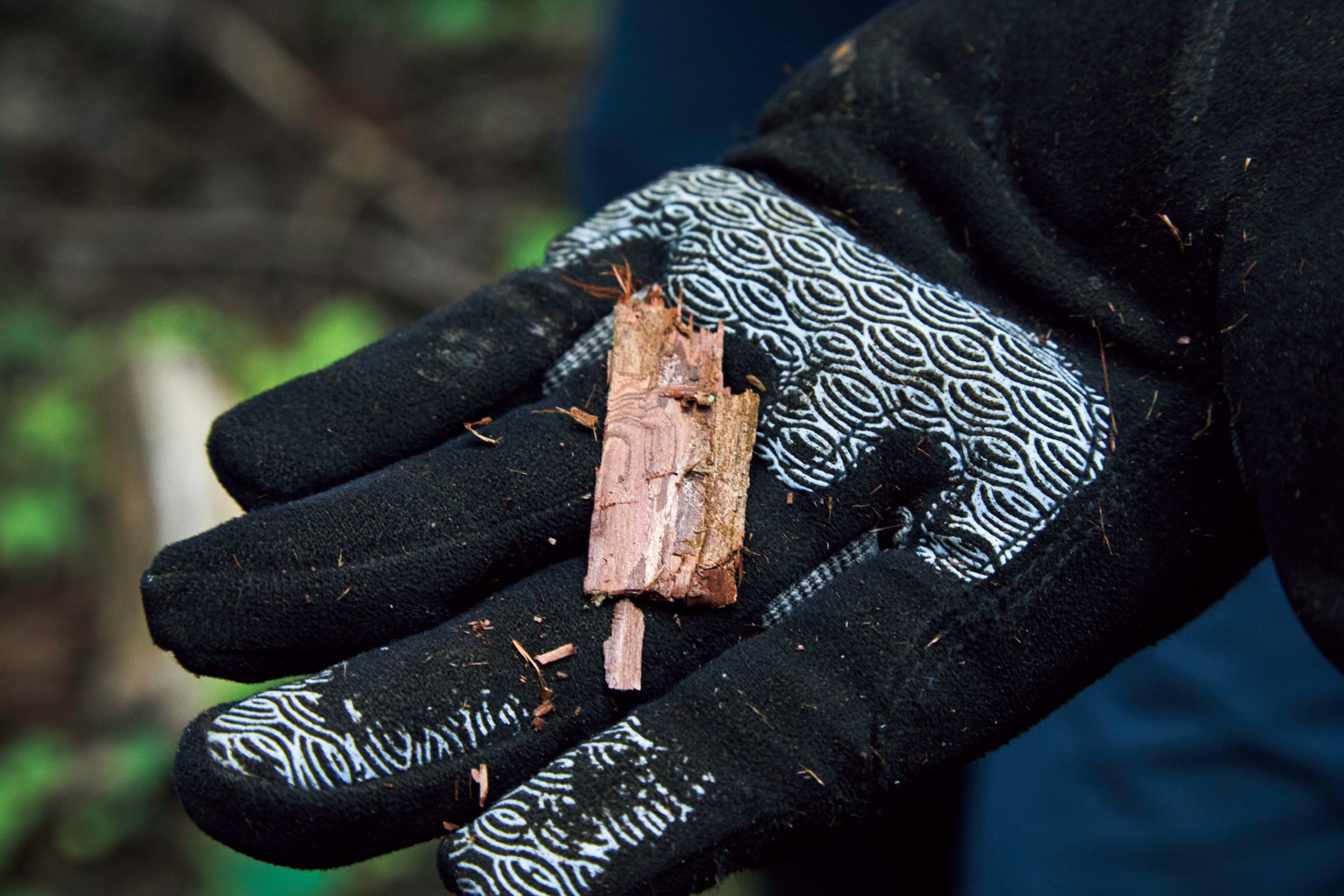
NOMURA Co.,Ltd. announced its "Fair Wood Support Declaration" in 2010. As a company that handles large amounts of wood in the creation of spaces, the company focuses on the legality of wood and the sustainability of the logging environment. By formulating the "Nomura Wood Procurement Guidelines," the company aims to provide clients with reliable products while also contributing to society by reducing illegal logging and deforestation as much as possible and leading to the protection and development of Japan's forests.
Currently, the company's Fair Wood activities have expanded to include a variety of initiatives, such as the "Wood Procurement Team," which is systematizing fair wood procurement across the company, the "Five Senses Group," which conducts demonstration experiments to see what effect wooden spaces have on people's minds, and the "Production Area Collaboration Team," which aims to deepen mutual understanding through interactions with production areas and create new value for wood together. Joint projects with other companies have also begun.
Akiko Umeda, a planner who works on the "Production Area Collaboration Team," is one of the people who has been working on environmental issues within the company from early on. She says that it was by chance that concrete exchanges with the Nishikawa lumber production area began against the backdrop of the "Fair Wood Support Declaration."
"Around the time the company made its declaration of support for Fairwood, there was a special exhibition and, as a planner, I wanted to try proposing local trees. However, I had no knowledge of wood, so I consulted with Fairwood Partners, a joint venture run by environmental groups, and they introduced me to Sorin, who said, 'Nishikawa lumber is a good choice.'
At the time, it was a small job, but the client liked the proposal because it was good for both the environment and society. On the other hand, the client was very concerned about things like splinters and insects. I didn't know the answer either, so I asked the people in the production area each time and communicated with them a lot. The finished product had a good presence and scent of wood, and the client was very pleased."
From this experience, Umeda believed that in order to make the most of wood as a material, users needed to have more knowledge about wood, so he planned an experience session for wood-producing areas within his company.
"First of all, it's important to go there at least once. So I asked the company to incorporate production area experience sessions into various programs. In 2020, we implemented a project called "Morimachi Door" as a subsidized project by the Forestry Agency.
We invited many creators from inside and outside the company to participate in a large-scale production experience event held in three locations: Hanno, Tama, and Owase. Wakabayashi-san coordinated the Hanno event, and that was the first time we collaborated with the Nishikawa lumber production area."
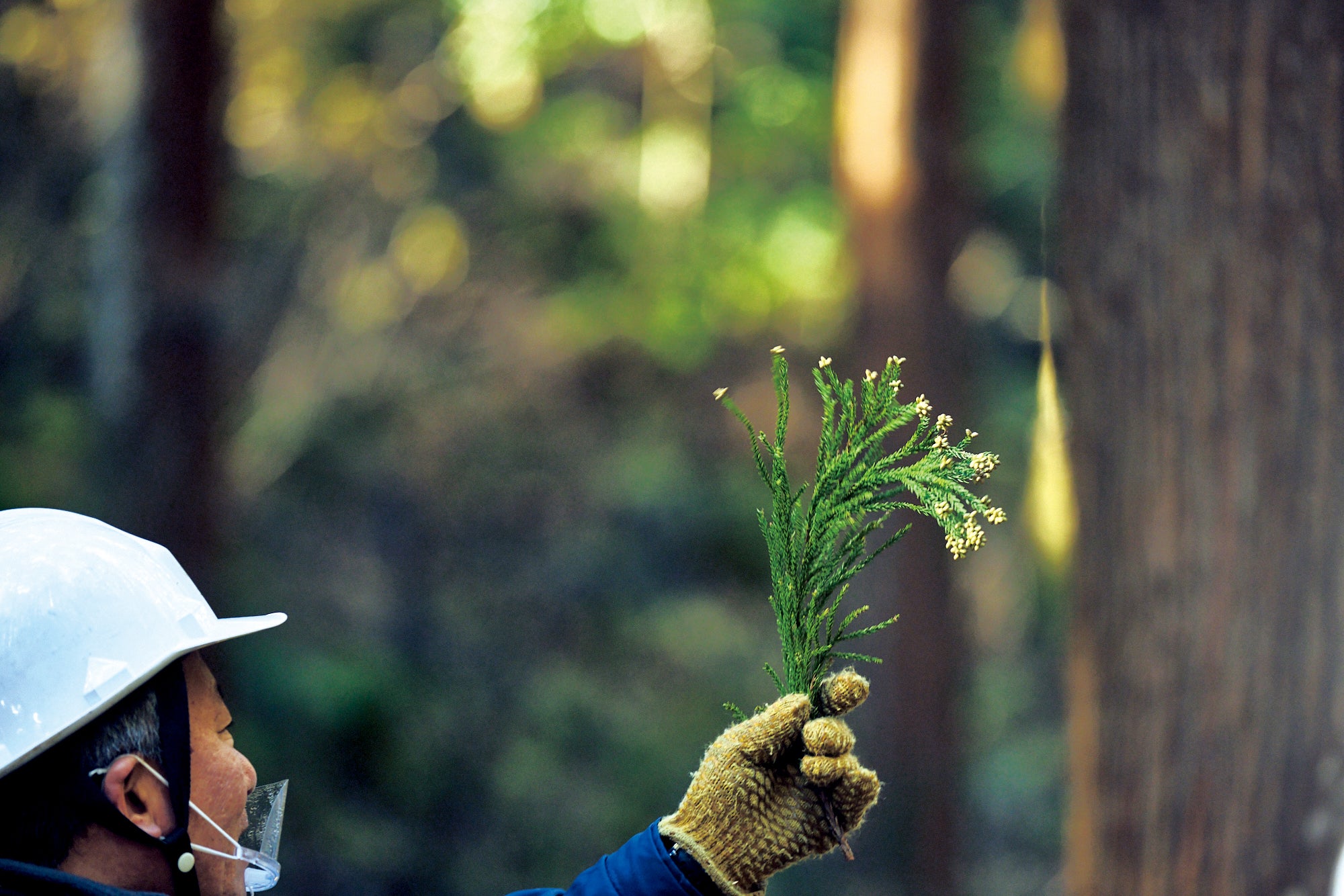
Not "I have to use it" but "I want to use it"
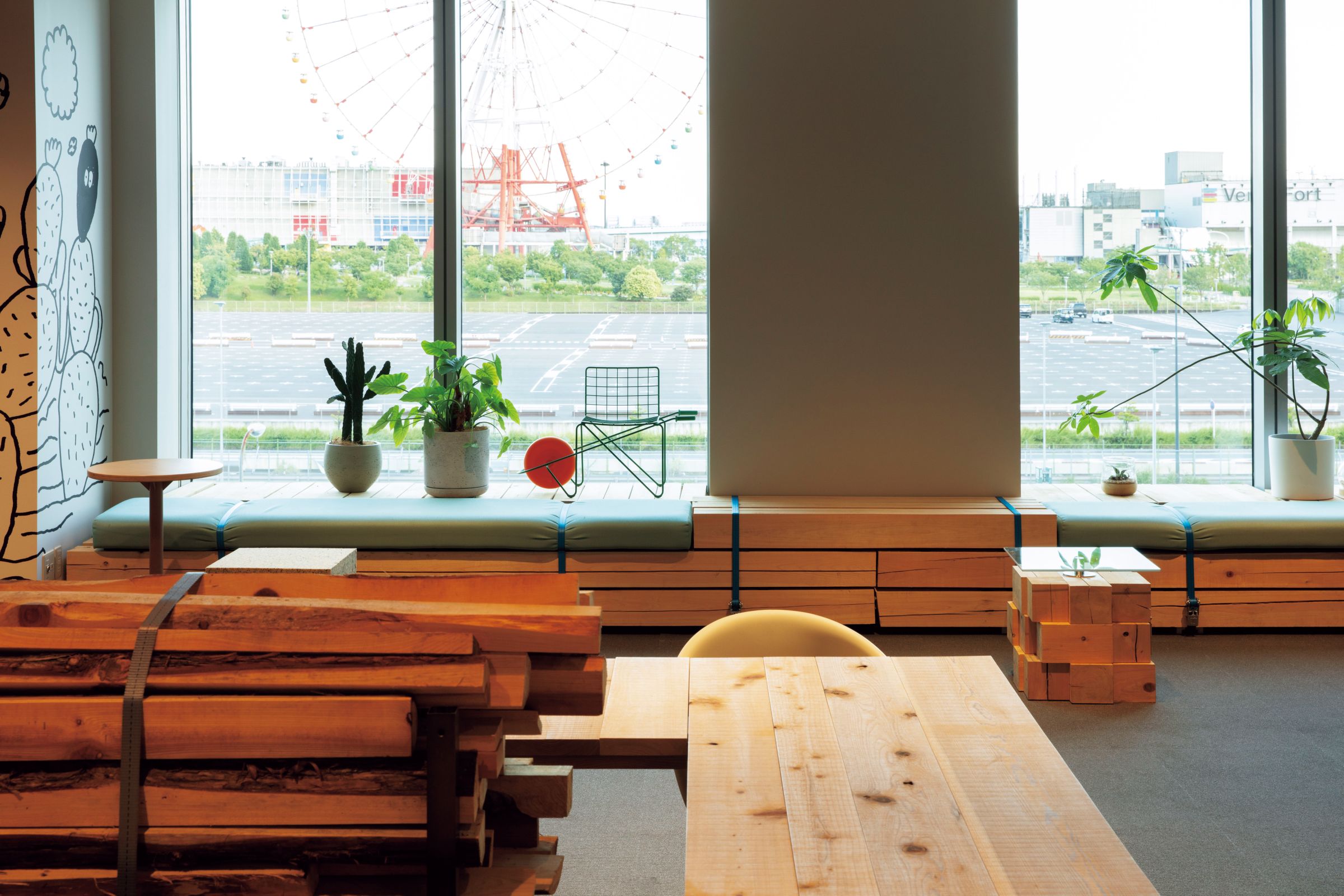
NOMURA Co.,Ltd. 's production area experience events have become so well established within the company that all new employees are invited to participate every year, but at the same time, the challenge of how to utilize domestic timber in actual creative endeavors remained.
NOMURA Co.,Ltd. designer Hirofumi Inoue felt the need to take Fairwood's activities to the next level.
"I decided to get involved because I can empathize with Fairwood's activities. However, the only example I've seen that actually uses domestic cedar and cypress is RESET SPACE_2 within our company. It seems that no one has yet taken it personally.
So, I wanted to change our own way of thinking, and after talking with Umeda, we decided to think about what we would like to experiment with with wood, not just take in what we have, and bring the tools and materials we need to the wood-producing areas, and create time to try and output something through trial and error."
RESET SPACE_2 is a communication space that was planned and concept design by employees themselves at Head Office of NOMURA Co.,Ltd., Ltd. in 2021. Reflecting the Fair Wood activities, domestic timber was used, and various mechanisms were placed throughout the space to help employees feel closer to domestic timber, such as benches made of bundles of drying timber, cedar and cypress balls shaped like those found in sake breweries, and samples of raw wood. Incidentally, the timber benches are a product devised by Asami of Nishikawa Baum, and are replaced with new ones every time the one-year drying period ends.
The local production team's activities to explore the output began with getting to work with their own hands.
"Our job is to create interiors, but because interiors materials are directly visible, if we use cedar or cypress, the color inevitably gives off a strong Japanese feel. For example, it would be difficult to use them in a Western-style hotel, and because they are soft, they are easy to work with, but they are also easily scratched. How do we overcome this?
"I decided to experiment with processing the surface, applying paint, and actually doing some hands-on experiments to see if I could bring out new appeal in cedar and cypress by tinkering with the look and concept design of the wood. I want to make it so that domestic timber is not something that we "have to use," but something that we "want to use."
The project is called "Tezain" (hand design) because designers who usually create concept design on computers are using their own hands to try out concept design.
NOMURA Co.,Ltd. designer Yukio Suzaka explains the significance of using his hands:
"I've always believed that humans are creatures that think by moving their bodies, so I usually draw as many pictures as I can and make models. In some cases, I even do some of construction myself.
So, I was impressed by the strength of wood as a material, and we all decided to try using our hands together, rather than just thinking about it. When you actually use your hands, you start to feel an attachment to the wood."
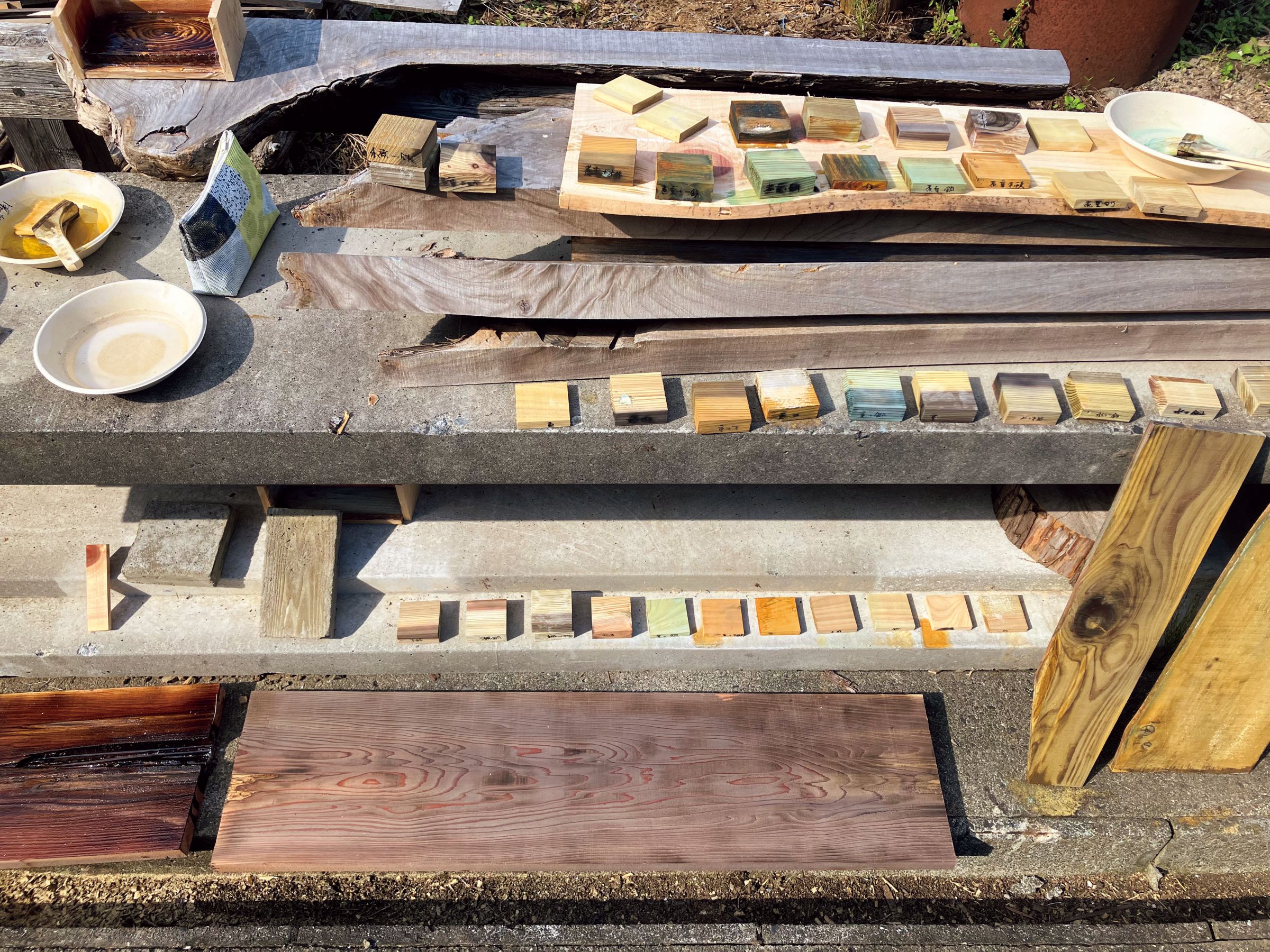
displays that makes you feel like you're walking through a forest
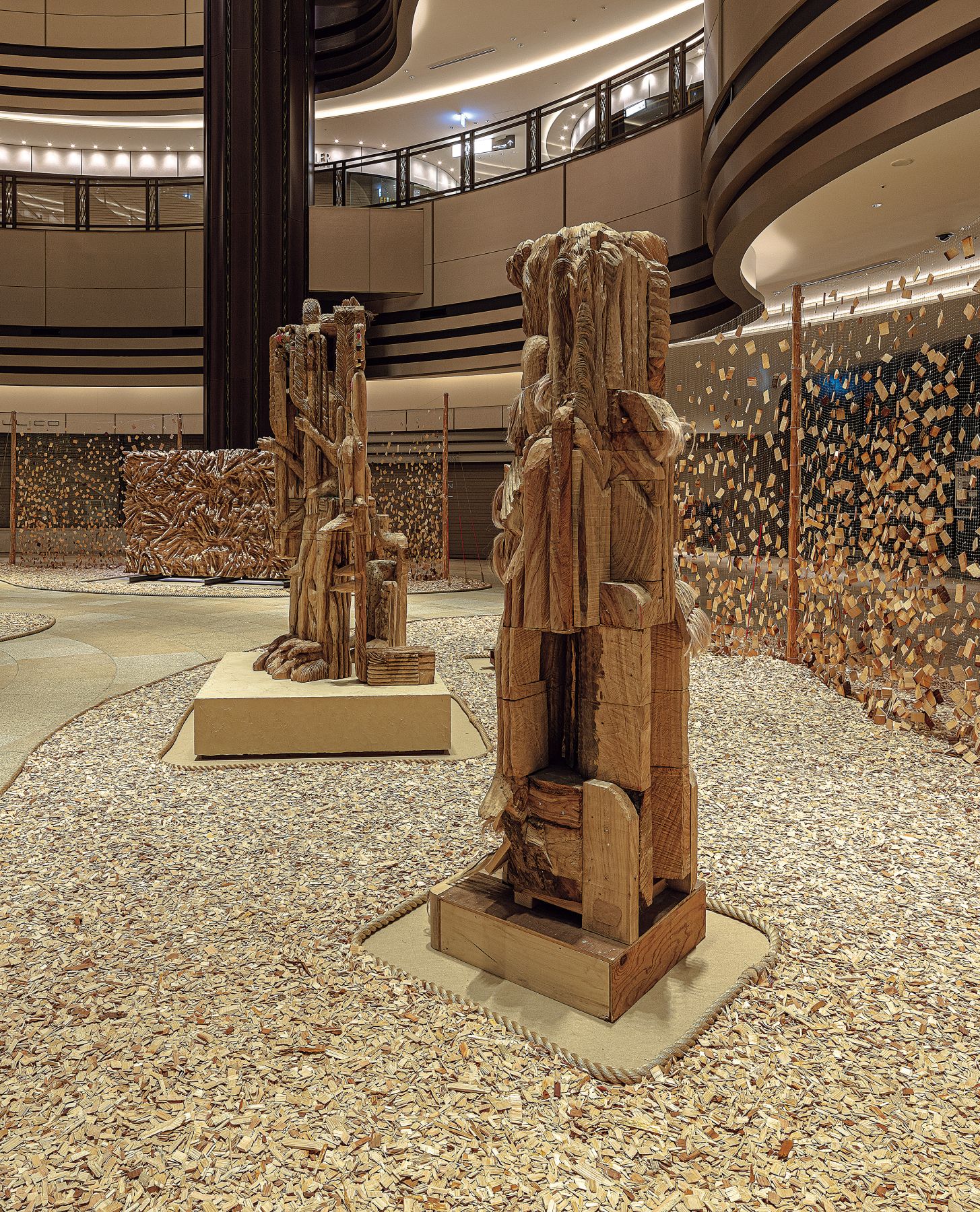
The "Hand Design" project is not aimed at producing any products, but at developing new know-how for utilizing domestic materials and stocking them as options for creating spaces. It has only just started, and there are not many prototypes, but nevertheless, unique "works" never seen before have appeared.
For example, flooring with tatami-like patterns carved into the surface of cedar boards. The shadows on the surface create a different look to the traditional Japanese style.
"Conifers are not very strong, so they are difficult to use for floors. They get dented and scratched easily, which can lead to complaints. So I came up with the idea to scratch the floor from the start, and make it look a bit like tatami mats. It feels good to walk on it barefoot." (Suzuka)
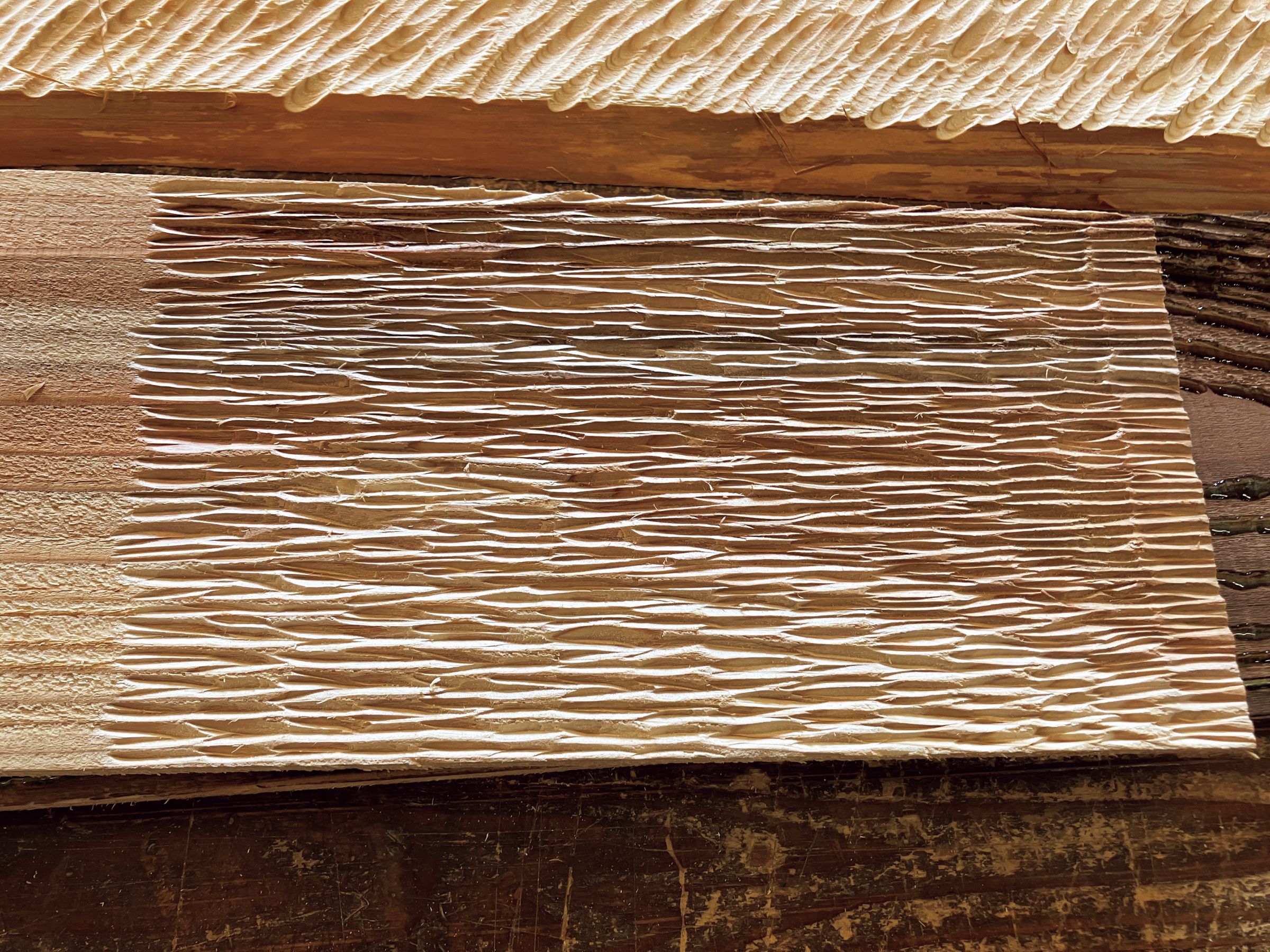
Or a pillar made by bundling thin scraps from a sawmill like square timber. Gaps are created between the scraps, creating a skeleton structure that allows visibility and breezes to pass through, and it can be used for interior decoration.
Designer Inoue says that the ideas for each of his "works" came from his visits to the places where the products are made.
"When I saw the scraps coming out of the sawmill, I wanted to use them for something. So I wondered if I could make it look like the 105mm square pillars that are the most widely available, and give it added value that is different from 105mm square pillars. I tried various things and came up with a function that makes it transparent. Lightness is also a valuable feature."
The first major project between the design team and the Nishikawa lumber production area was displays production for the event "Living with Wood" held at Tokyo Midtown Hibiya in April 2024.
The design team envisioned a space that would make one feel as if they were walking through a forest. Wooden sculptures made by artists were placed in the open atrium, and each sculpture was presented as if it were standing wrapped in wood chips. When you step on the wood chips to approach the sculptures, the scent of wood fills the air, creating a soothing atmosphere that you wouldn't expect in a building in the city center.
During the production process, detailed discussions were held repeatedly with the production area to determine how to realize the design team's concept.
"I wanted to create a curtain of flying wood chips around the sculpture. I attached a lot of wood chips to a net about 3m wide, but the wood chips made by regular machines are too small.
From deciding the size of the chip to how to attach it to the net and how to set up the net, we tested it together and decided each step by sharing our ideas. If we didn't have a regular relationship, we wouldn't be able to make it just by receiving the blueprint."
Manufacturing becomes more fun!
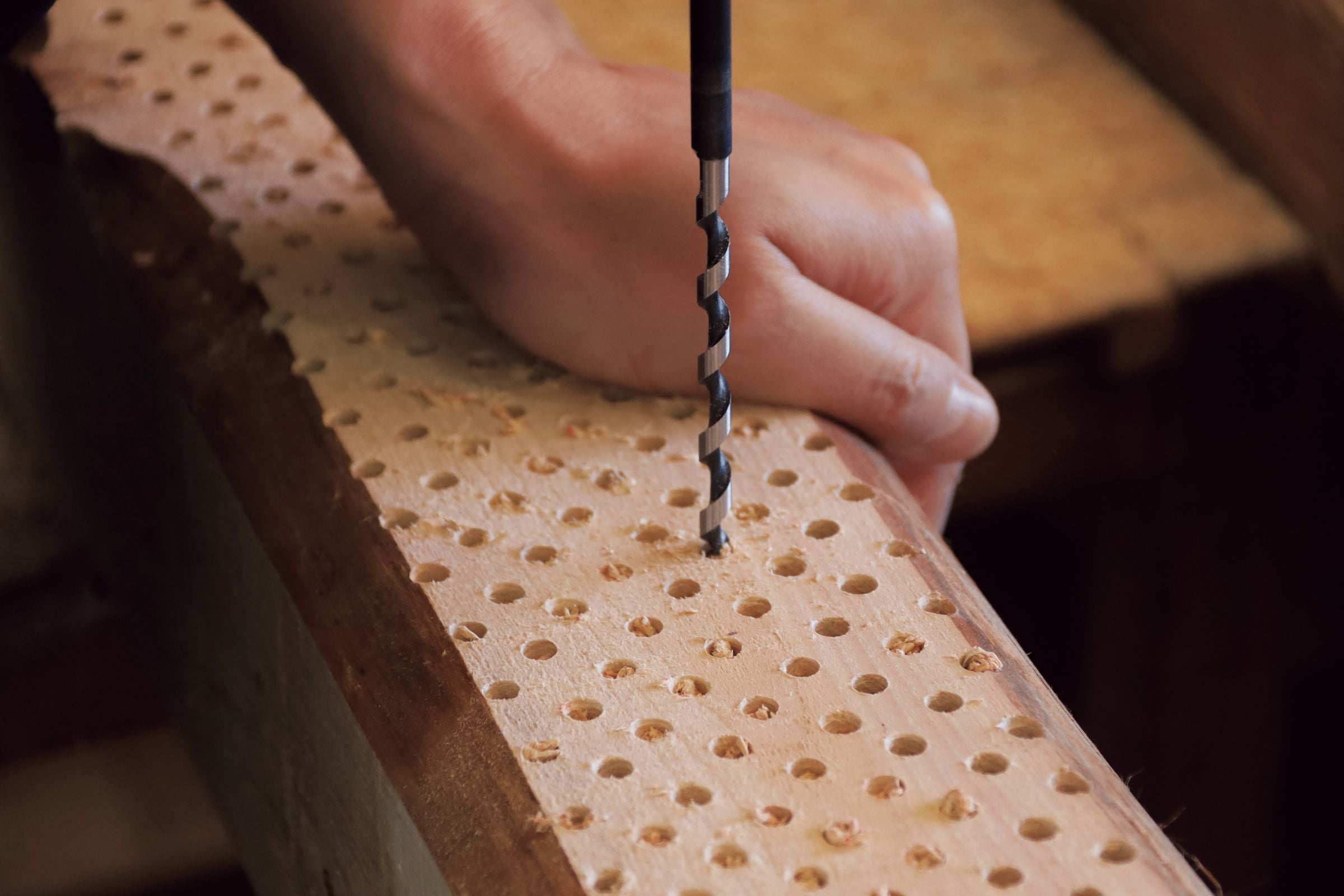
concept design and blueprints are made on a computer, and specifications are decided by selecting standard products from samples from material manufacturers. What kind of changes will collaboration between those who make wood and those who use it bring to this routine in the construction industry? Inoue, the former president of Sorin, hopes that manufacturing will become more interesting.
"Recently, I had the opportunity to exchange opinions with an architect, a carpenter, a lumberyard, and myself, a forestry worker. In today's architecture, the design is submitted first and everyone works according to it, but if we were to be involved from the planning stage, we would be able to propose things to the carpenters, lumberyard, and forestry workers, and we would be able to come up with ideas. We all agreed that we could create something better.
So if you tell us what you want to create and tell us your initial concept, we can send it to you. I think that if we can have a dialogue with the concept design, we can create something incredibly interesting."
Wakabayashi of Nishikawa Rafters says that the uses for non-standard timber are expanding.
"Standardized timber is stocked to a certain extent because distribution volumes can be expected. But if you want to use special timber that does not meet these standards, it has to be harvested from the forest. Only by communicating with the users and the producers can you learn what is in the forest and how long it can be used after it is harvested. And once you understand this, it will open up new uses for the timber."
And above all, there is a possibility that awareness in the production areas will change, says Shuntaro, president of Sorin.
"When you're deeply involved in the world of wood and forestry, there are ideas that you would never think of. I guess my mind is limited to traditional ways of using things, like in Japanese-style architecture. I'm really grateful for the interaction with users, because it helps me to break that mold and gives me innovative ideas."
On the other hand, Umeda of NOMURA Co.,Ltd. says that it has been significant for those who use wood to have more imagination about the place where it is produced.
"By visiting production areas, you can start to imagine what it's like to be on the production side. For example, if a designer who likes black wood hears that black core is not popular, they might end up causing a problem by asking for 10 pieces of it. If you learn how black wood comes from a lumber mill, you also understand how difficult it is to collect it. If you want to use it, you have to discuss how to collect it in a way that is good for the production area.
As the exchange progressed, everyone gradually became able to imagine such things, and the value of concept design increased. I'm thinking about creating a place in Hanno where people from the production area and creators can interact on a daily basis and make various prototypes together."
Even as times have changed from the Edo period to the present day, Hanno remains a timber-producing area close to Tokyo. People who are trying to explore new possibilities for wood as a material are beginning to gather there.
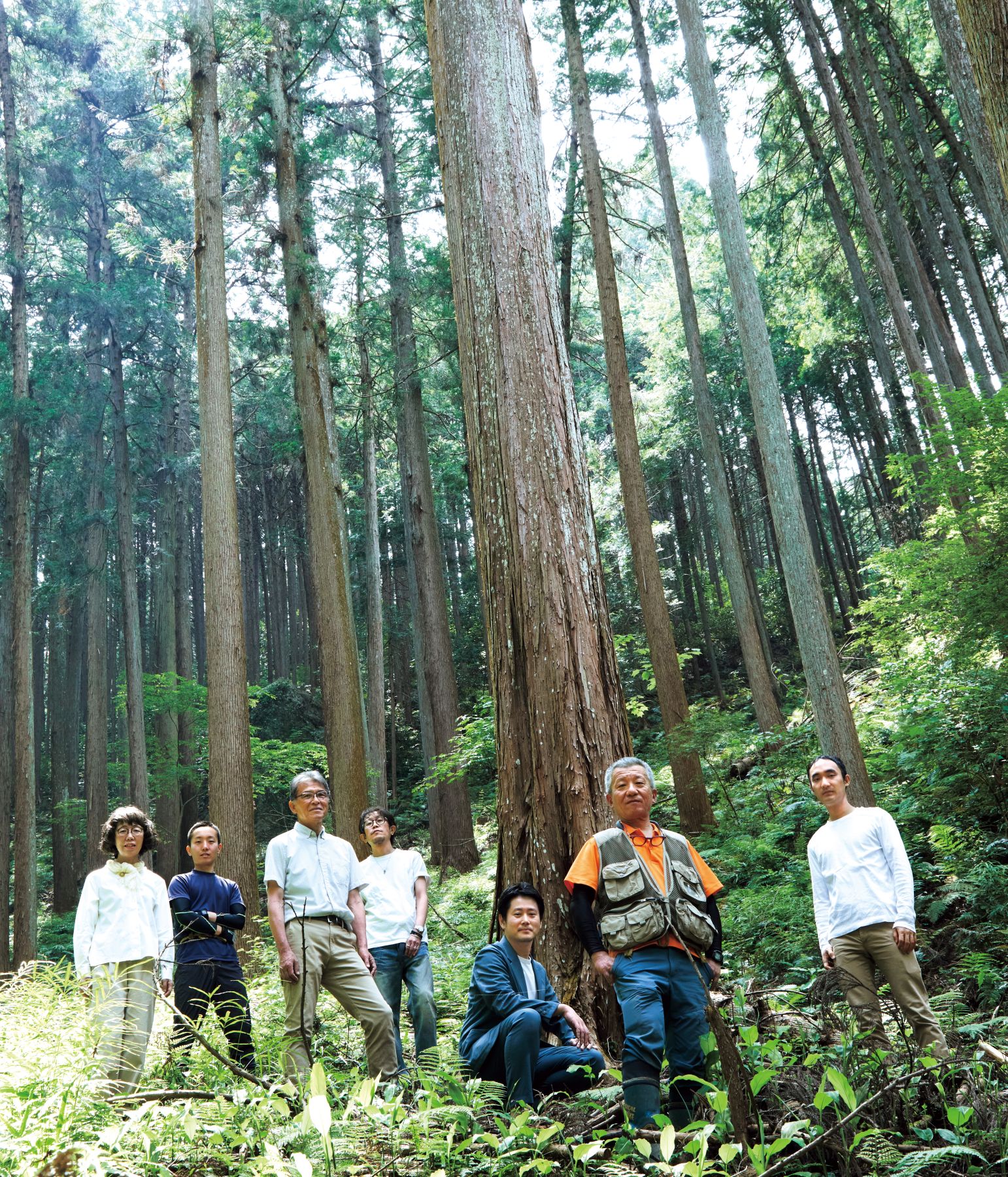
(Interviewed in June 2024. Titles in the article are those at the time of the interview.)
Interview and text by Tsuyoshi Nose (former editor-in-chief of Nikkei Trendy)
Photo = ©Kenta Yoshizawa
profile
Forest Creation
Former RepresentativeJunji Inoue
Forest Creation
representativeShuntaro Inoue
Nishikawa Rafters
representativeTomonobu Wakabayashi
Nishikawa Baum
representativeYuji Asami
NOMURA Co.,Ltd.
Creative Headquarters Future Creation Research Institute Sustainable concept design Lab PlannerAkiko Umeda
NOMURA Co.,Ltd.
Creative Headquarters, First concept design Center, concept design Department 4, Inoue Room, Room ChiefHirofumi Inoue
NOMURA Co.,Ltd.
concept design Director, concept design Department 5, First concept design Center, Creative DivisionYukio Kazusaka
NOMURA's Media
- NOMURA Co.,Ltd.SCENES
Please contact us using the button below if you have an inquiry, want to request a quote or request documents.
We have created a separate “FAQ page” that lists the most common questions we are asked.
Please take a look at this page if you have a question.