─See and touch the world of Ghibli
- #Chubu
- #digital technology
technology & engineering
Ghibli Park "Howl's Castle"
Nagakute City, Aichi
Creating animated stories in the real world
In March 2024, Ghibli Park opened a new area called "Witch's Valley." The European-style townscape, inspired by Studio Ghibli works featuring witches, features the Rock-Paper-Scissors Bakery and Okino House from "Kiki's Delivery Service," Hatter's Hat Shop from "Howl's Moving Castle," and the Witch's House from "Earwig and the Witch." In a secluded corner, Howl's Castle stands as a living, imposing figure, just like the world of the film. What kind of ingenuity and challenges were involved in realistically representing the worldview of an animated film in an actual building? We spoke to members of NOMURA Co.,Ltd. team responsible for the creation of the building.
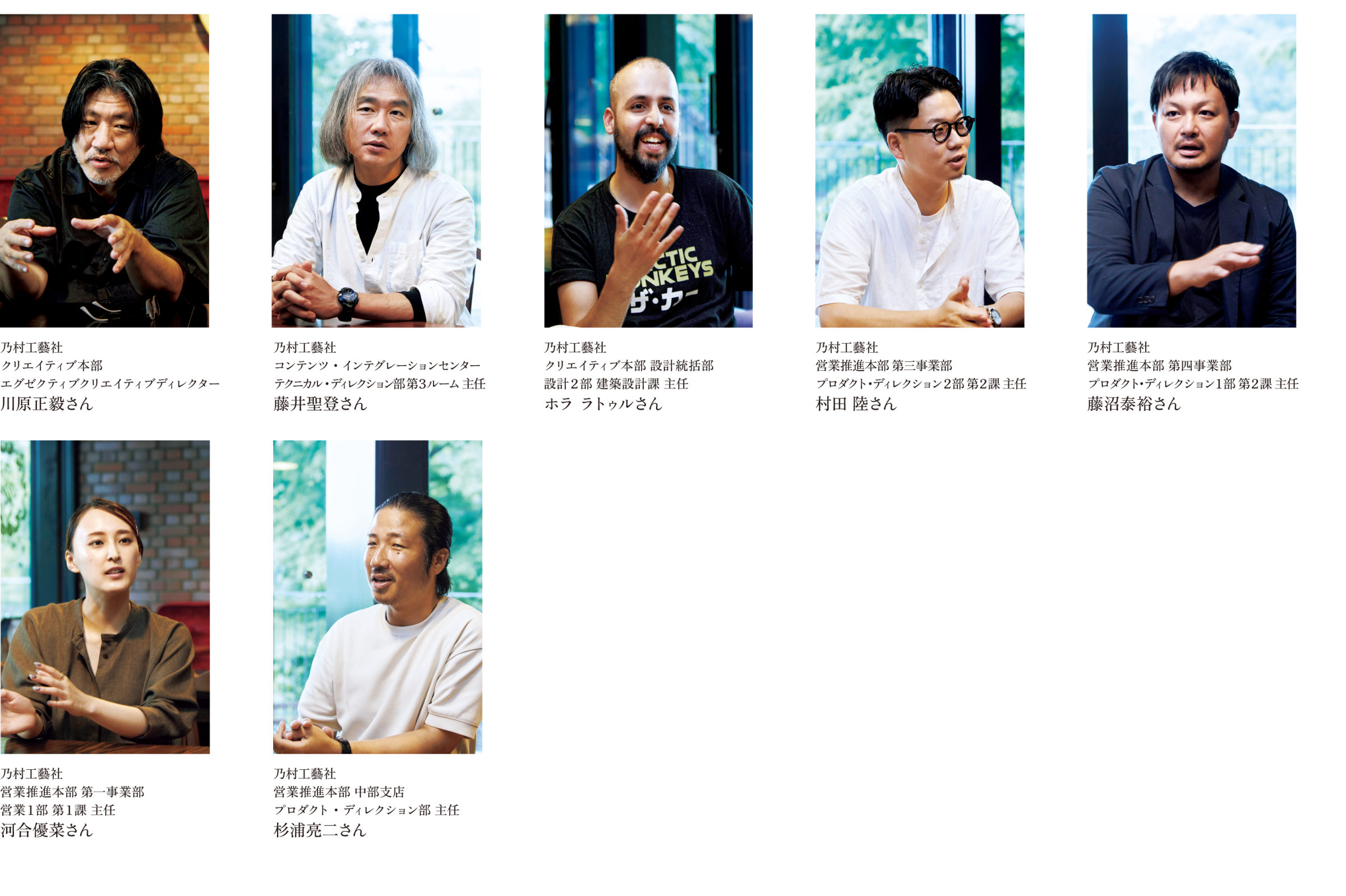
Not crafts, but suspicious industrial products
The first step in the project was to create sketches to create a three-dimensional concept design for Howl's Castle, which is depicted in two dimensions in the film. Executive Creative Director Masaki Kawahara, who is also in charge of NOMURA Co.,Ltd. team, worked closely with Director Goro Miyazaki, who oversaw the overall production of Ghibli Park, to refine the image.
"The creative work with Director Goro started as a trial and error process. First, he had a concept design drawing of a three-dimensional drawing. While looking at that, I drew a sketch with various details that were faithful to the image of the castle that appears in the movie. Then, he responded, 'That's not it,' and I thought, 'Huh?' Then he shared the background story with me.
This castle is a continuation of the final scene of the movie, where Howl and Sophie fly away after various events in the story. As the story progresses, the things that were attached to it fall away, the unnecessary things are stripped away, and in the end, it comes down to this valley as a place of peace. So, it's not like the monster castle that appears at the beginning of the movie. So, I started the sketch again from scratch and redrawn the castle with a gentle expression.
Kawahara's sketches were sent to Director Goro, who would then add correction instructions in colored pens and send them back. This back-and-forth process was repeated endlessly for about six months to a year for each part of Howl's castle. An important theme there was not just to fill in the form, but also to consider how to create a sculptural taste. Kawahara says,
"Because copper plates are used extensively, at first I was thinking of it as a metal craft. But Director Goro thought it was something different. He wanted it to be, for example, a Russian armored cruiser. In other words, it wasn't a craft, but a rough industrial product. He had the image of a suspicious industrial product made by putting together thick lumps of iron or copper. So I was able to get a feel for it and start creating concept design."
Incorporating the worldview of the work into the blueprint
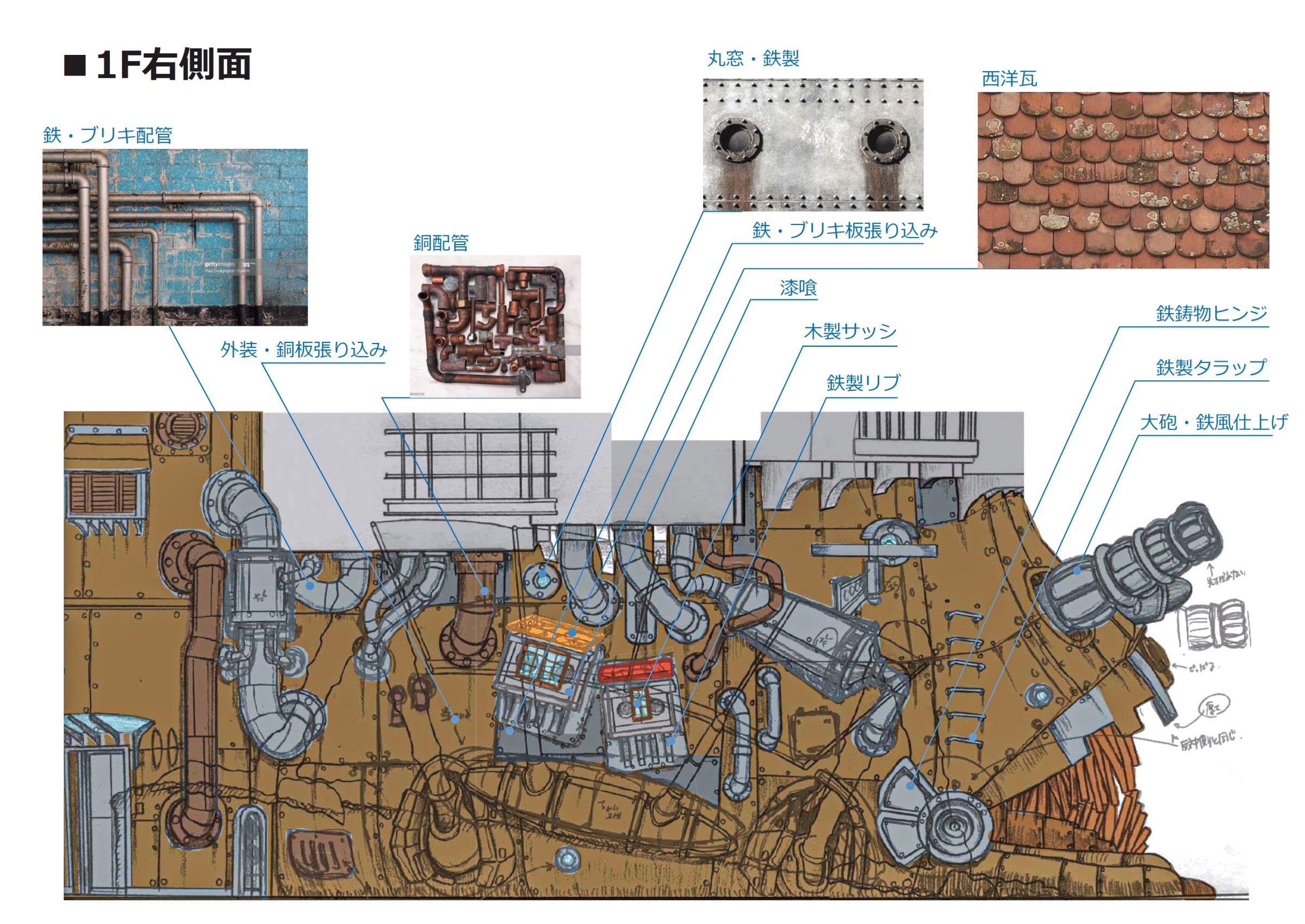
The team worked on drawing up Kawahara's sketches. First they drew 2D drawings, then they made 3D drawings. The design was mainly done by Fujii Masato, head of the Technical Direction Department's 3rd Room, who was in charge of the sculptural design, and by Hora Latour, head of the design administration Section of the Design Department 2, who was in charge of the structural design. When Fujii first saw the sketches, he felt they would be difficult to work with.
"I've been involved in making a variety of things up until now, but I thought it would be difficult to materialize the worldview that was set in this work. As Director Goro said, it has to be the next image after the last scene of the work. I drew the line at that point in my design interpretation. I had to think about how to fit it all together, but in what form and how to present it. That's because I had to put that into the blueprint."
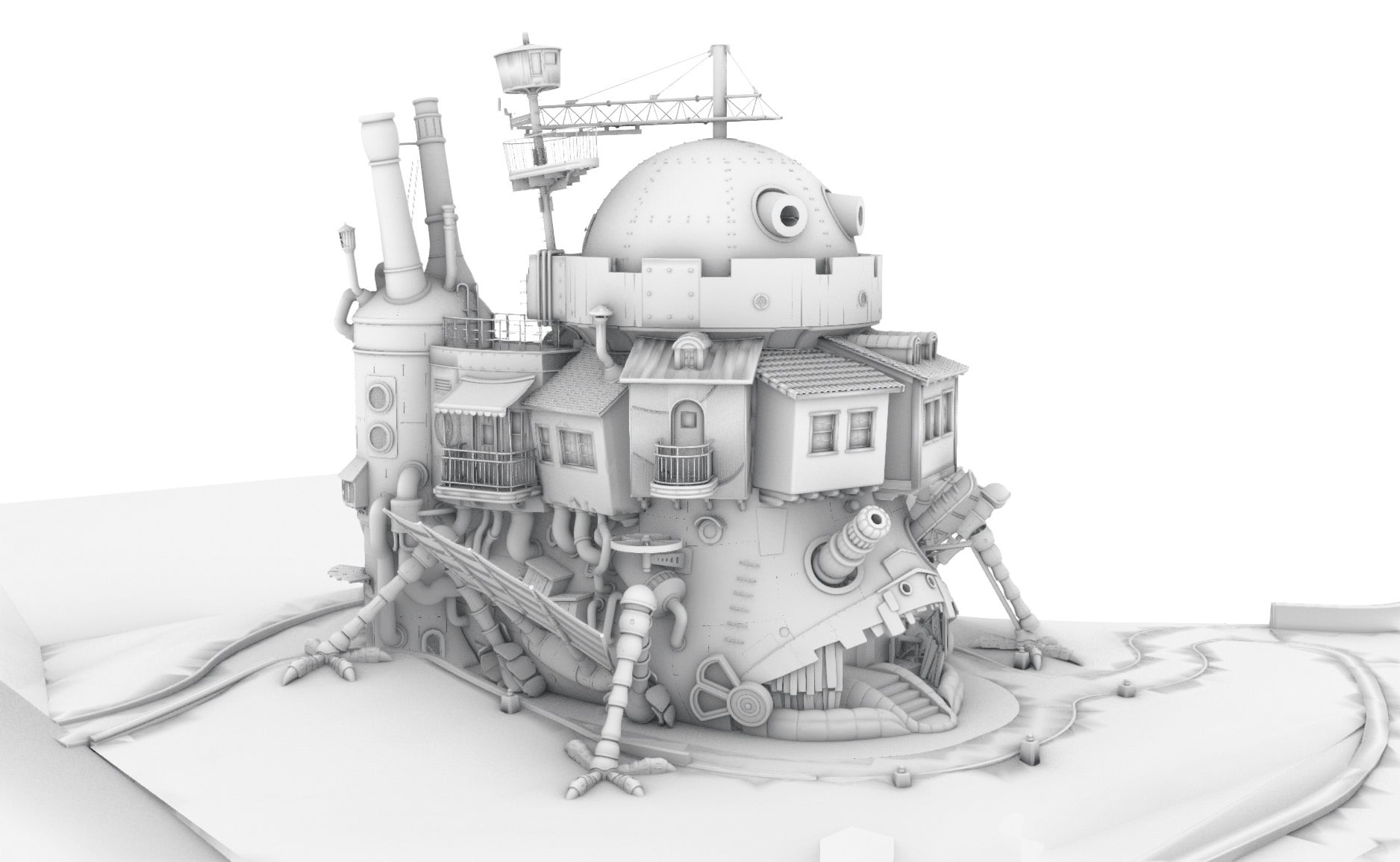
Hora, who was in charge of structural design, felt that the project was difficult in a different sense.
"I got involved from the working drawings phase, and as a preliminary step we analyzed things like earthquake and wind resistance. But because Howl's castle has a very organic shape, we were concerned about the standards used in regular architecture.
For example, wind pressure is calculated using the maximum area of the building's front, which is called the projected area, but the projected area of Howl's castle is not immediately known. So, using new software and studying it myself, I developed software that can analyze organic shapes as well."
Howl's Castle was built as a structure that allows visitors to enter. It has a concrete structure on the inside with sculptures attached to the outside. The entire structure, including the sculptures, meets the architectural requirements. The overall design and structural and equipment design was handled by Nihon Sekkei, the overall construction was handled by Kajima Corporation, the prime contractor, NOMURA Co.,Ltd. was responsible for the design and construction of the exterior sculptures and mechanical parts and the demonstrations inside the building. All the companies involved, including Studio Ghibli, worked together to tackle the project's challenges, discussed solutions, and moved forward with production. Hora continues:
"Because of the castle's complex structure, we didn't just use software analysis. Nihon Sekkei and Kajima Construction built a model and conducted wind tunnel tests. They found that the load on the two chimneys sticking out at the rear of the castle was higher than the design value. With an organic structure, the way the wind hits the structure is completely different. We revised the design based on the results of the wind tunnel tests."
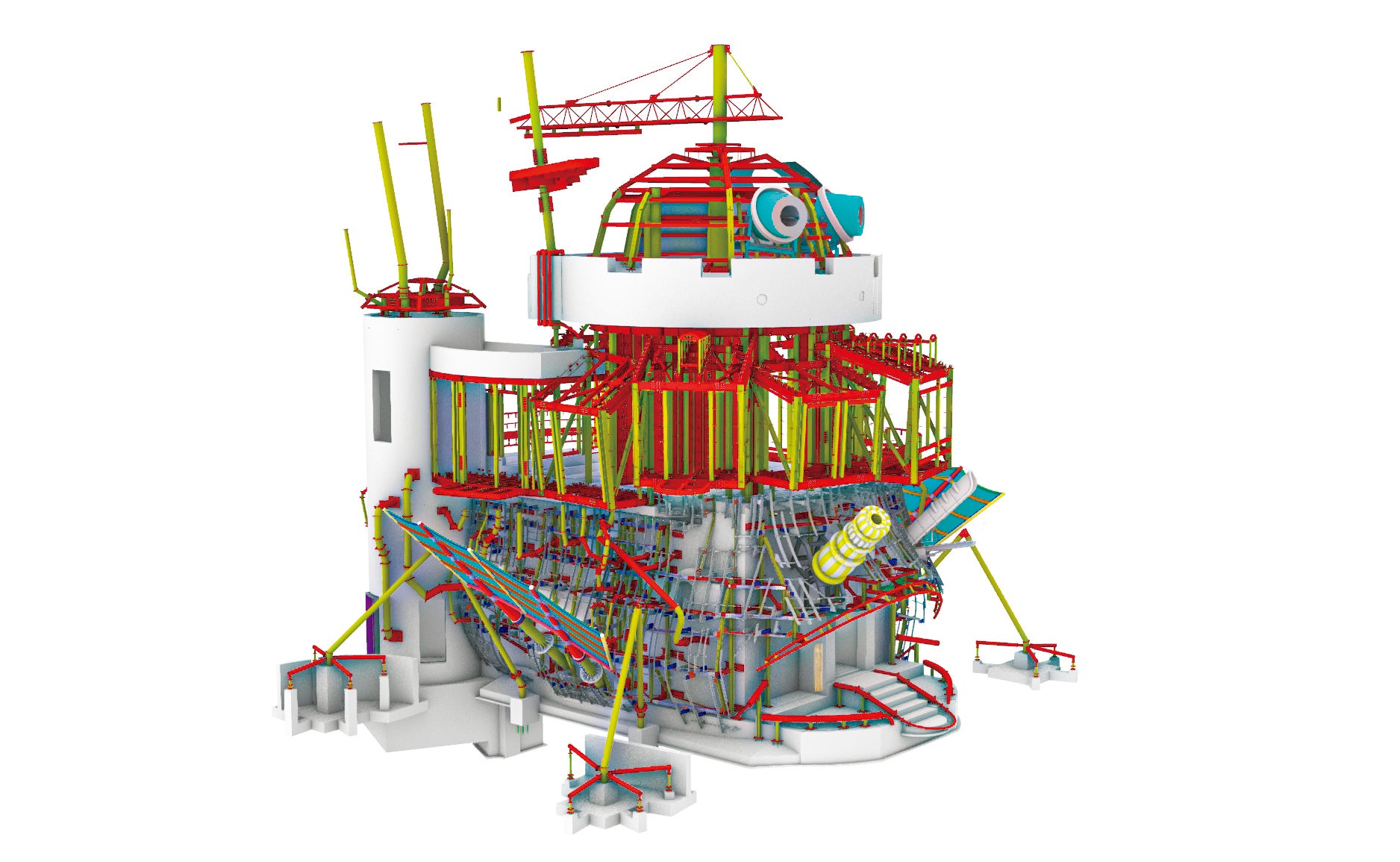
Riku Murata, Product Direction Division 2, Section 2 Chief, was responsible for compiling the design and structural designs into drawings and coordinating them with Kajima Construction and Nihon Sekkei. When Murata joined the team, he was immediately faced with the task of designing the steel frame.
"When I joined the project, the shape of the structure had already been decided. However, an enormous number of steel beams had to be attached to this structure to support the exterior structural panels. Kajima construction was responsible for attaching the steel beams to the structure, but NOMURA Co.,Ltd. team designed the steel beams one by one to match the exterior structure. Then we had to coordinate with the structural engineer at Nihon Sekkei.
In the end, except for the elevator area at the back, the body of the structure is fitted with eggplant-shaped steel beams, which resemble a deformed semicircle. There are an incredible number of them, but because the shaped panels they are attached to are all different, no two steel beams are the same shape."
Use real things whenever possible
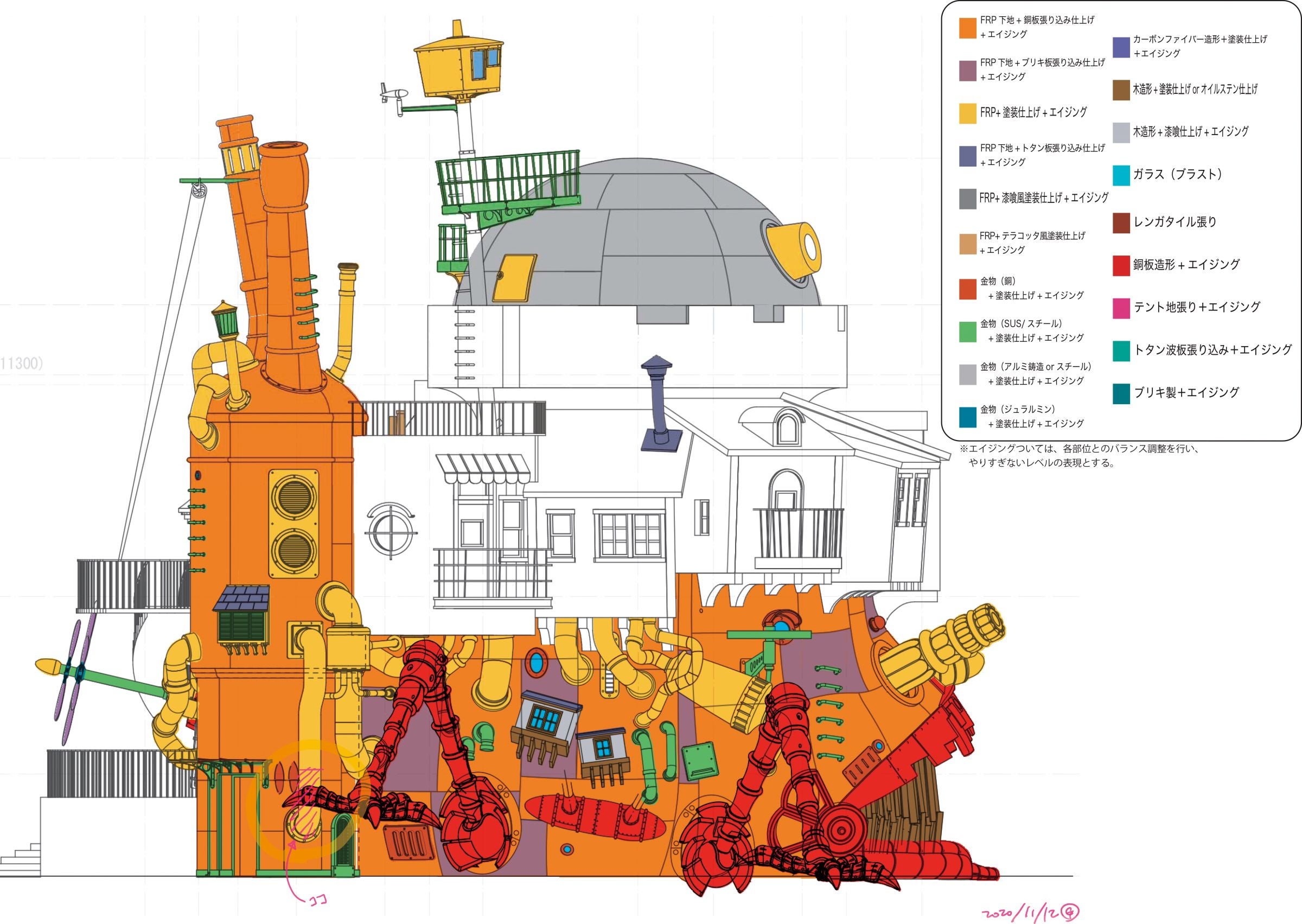
When creating something from blueprints, there are many things that must be considered on-site, such as construction time and budget management. In the case of Howl's Castle, the first big task was to select the materials. Fujinuma Yasuhiro, head of Product Direction Division 1, Section 2, who was the first person to join the project as the production manager, said he was racking his brains over how to create the worldview of the work.
"Director Goro's wish was to use as much of the real thing as possible, so we used metal wherever possible. For example, the top gun dome is cast from aluminum, taking into consideration the texture and weight. It's all assembled from panels cut from molds. It's an unusual construction.
The panels around the body and the legs are copper plates. Although we used FRP in some parts for weight, safety, durability, construction time, and cost considerations, 90% of the materials used for the modeling became metal.
The choice of materials is directly linked to the planning and concept design, so we worked it out as a team and put together a proposal for Director Goro."
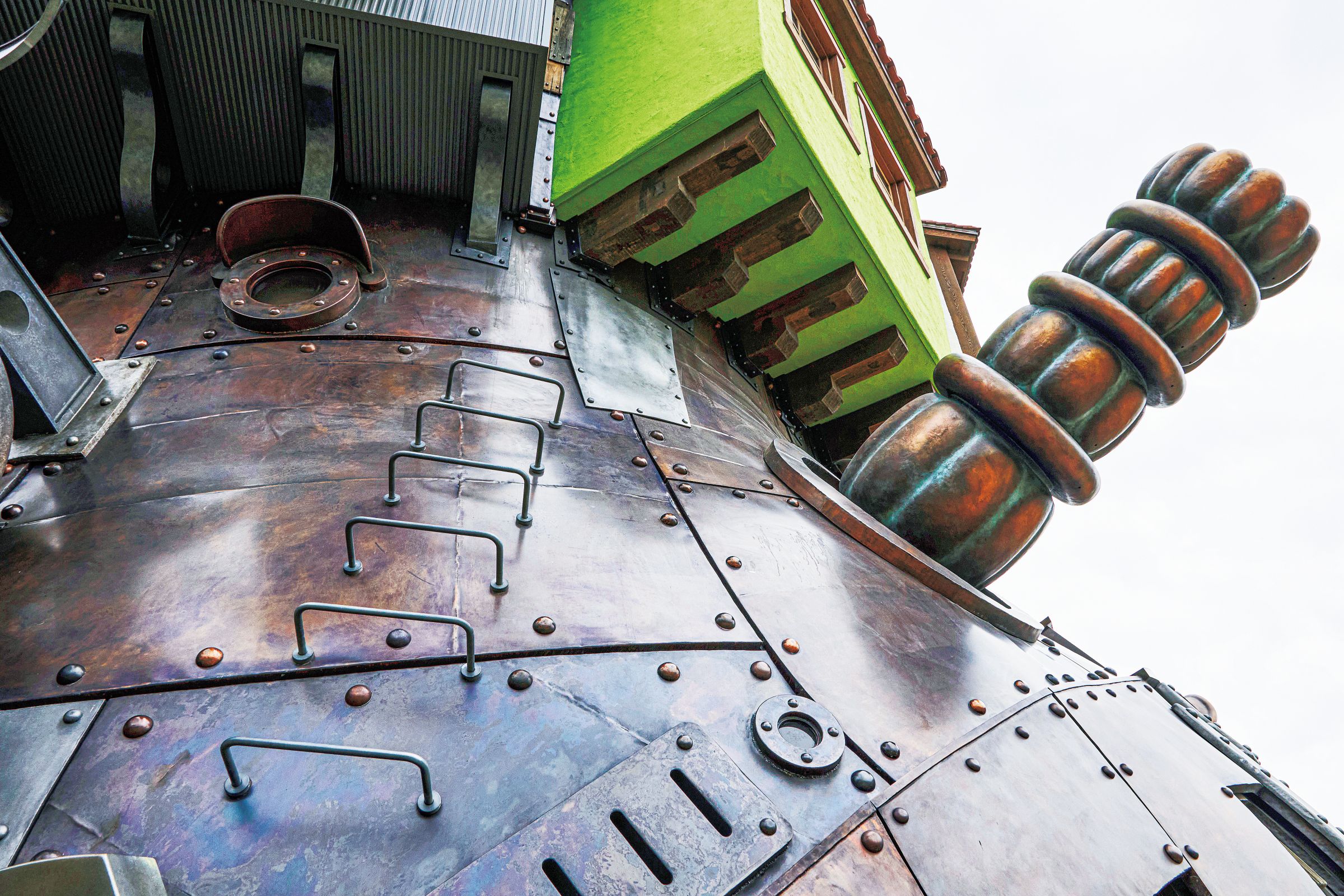
In parallel with the selection of materials, the construction schedule and selection of subcontractors were also carried out.
"Because this was a project with such complex shapes and materials, and above all, the worldview was important, we had a hard time choosing which companies to work with. There were so many parts, so we ended up working with 55 companies. Just the ordering process was a lot of work. We also had to work closely with Kajima Corporation and Nihon Sekkei, and get their approval as we went along, so it was difficult to get the job done smoothly.
Above all, the final image of the finished product is in Director Goro's head, so we can't move forward unless he is satisfied with it. It was difficult to figure out how to schedule and confirm that."
Yuna Kawai, Chief of the First Section, Sales Department 1, said that while supporting this production effort as a sales representative, she realized that the creation of the product had finally begun.
"At first, this project started with just Kawahara and concept design team and the sales team. We made progress by polishing the concept design sketches, but because this was an unprecedented project, the sales team didn't really feel like we could actually make it into a reality. But when Fujinuma joined the project at the beginning, he drew up a master process. When we took that process chart to Kajima Construction, we thought we might be able to make it. From then on, more and more of the team joined the project, and we gradually fleshed out the image of Howl's castle. It felt like the creation of the project had just begun."
The most interesting thing is that nothing can be done
construction of the structure involved panels made in a factory based on 3D blueprints, transporting them to the site and assembling them on the outside of the structure. However, this was fraught with difficulties and ingenuity. Ryoji Sugiura, head of the Product Direction Department at the Chubu branch, who oversaw the on-site construction, explains:
"The details and shape of the panels are made in the factory, so they are perfectly finished, but the difficult part was how to install those organic shapes on site according to the blueprints. It's not just a matter of fitting them into a predetermined location. Naturally, there are discrepancies between the dimensions of the blueprints and the dimensions of the structure, and when making the panels, they are made to have a lot of "escape," or movement, so precise positioning was necessary to fit them neatly into the designated place.
Especially the gun dome and the fuselage panels. For the fuselage panels, data was created on a 3D drawing for each of the four points, so we received numerical values for the XYZ coordinates of each point from the design team, and we measured them on-site while assembling the panels. There was always a surveyor there, and he measured the positions of the four points. It took much longer than installing a normal curtain wall or exterior wall."
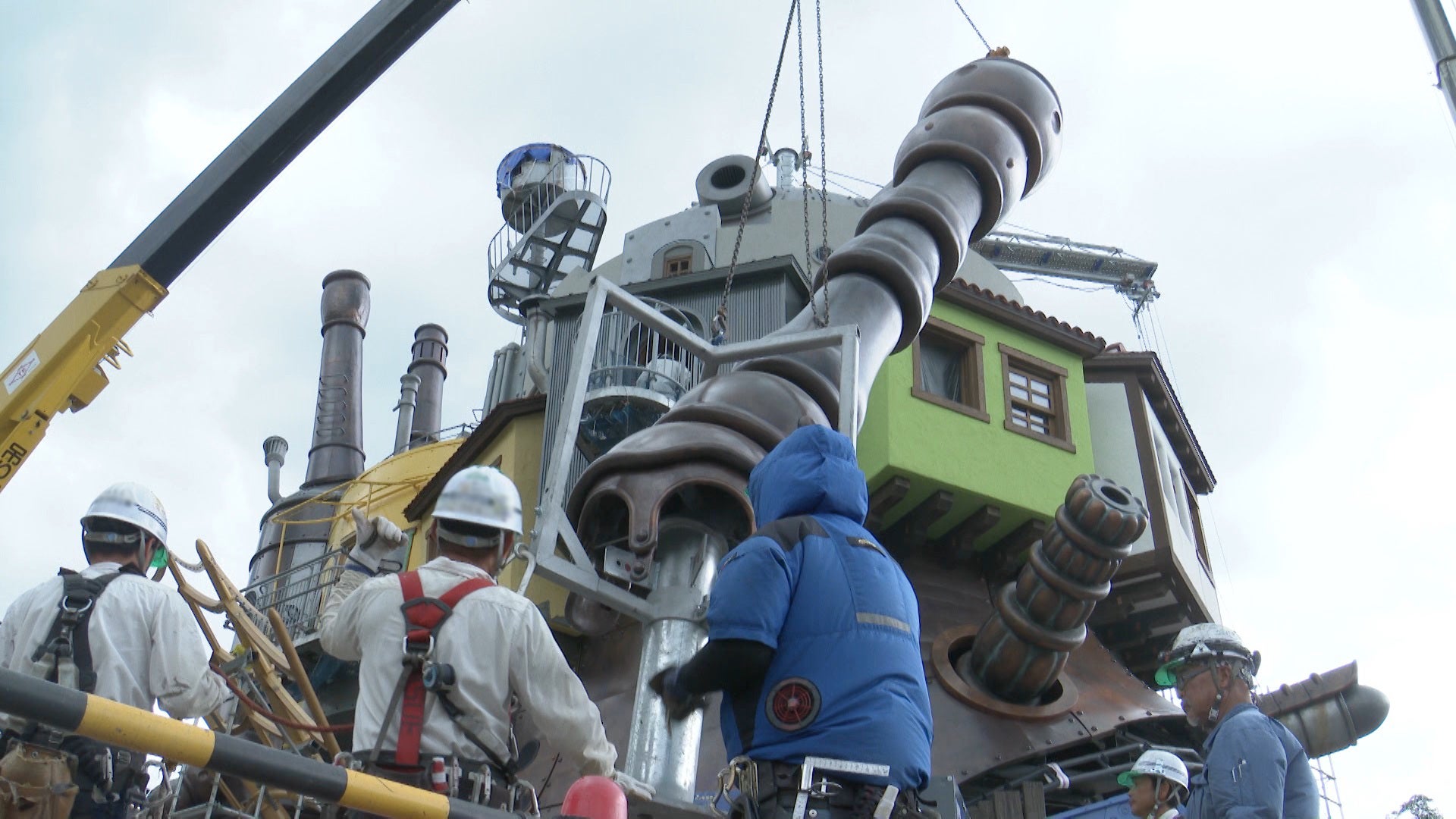
Although the exact position was determined, the installation work was another challenge.
"We designed it so that the installation work could be done properly while checking in 3D, but it meant that someone had to get behind the panels to fasten them. There was only a small gap between the structure and the panels, so they had to get in there and fasten the metal fittings one by one. The craftsmen had a hard time. Fitting things exactly where they should be was a very difficult task at this site, even though it may seem simple.
Even so, when we were assembling it on site, we would sometimes find ourselves thinking, "Huh?" In those cases, we would cut it on site, but the team would brainstorm ways to avoid creating an unnatural shape. The conflict between the base of the left leg and the lower panel of the stairs was quite difficult. The legs were installed first, and when the staircase panel was installed, it interfered with the legs and the panel would not fit. We were running out of time for the deadline, so we had no choice but to cut the panel."
However, leaving the panels cut would have ruined the design, so it was Fujii who worked with Sugiura and the others to find a solution.
"The staircase panel had been cut, so there was a hole in it. It clearly looked like a building. We were discussing what to do, and when I consulted with Director Goro, he didn't give me any specific instructions, just told me to do it well. It was towards the end of the project, so I think we had communicated well up to that point, which is why he left it to me.
So, thinking about the shape of the castle, I thought it would be good to make it look alive, since it is a living thing. I suggested to Director Goro that we make it look as if the legs are hitting the wall and there is some movement as if it is crumpled. The director gave us the OK, so we quickly tried it.
As a result, it feels like Howl's castle now has one more attraction, and it's been well-received. After all, the most interesting part is the "insignificant part." The parts that we all came up with together on the spot have a nice flavor to them."
Incidentally, because of the intricate and complicated structure, interference was bound to occur. Hora says that Fujinuma checked the 3D images every day to take precautions against this, even if only a little.
"Mr. Fujinuma checked the 3D drawings one by one every day. If there was interference between the structure and the structural panels, we couldn't just cut away the concrete of the structure, so we had to change the structural panels. We also worked closely with Nihon Sekkei, and because this was a building that had gone through the procedures required by the Building Standards Act, we had to share any design changes with the other companies involved. It was quite a lot of work."
Creating a "collection feel" at the production site
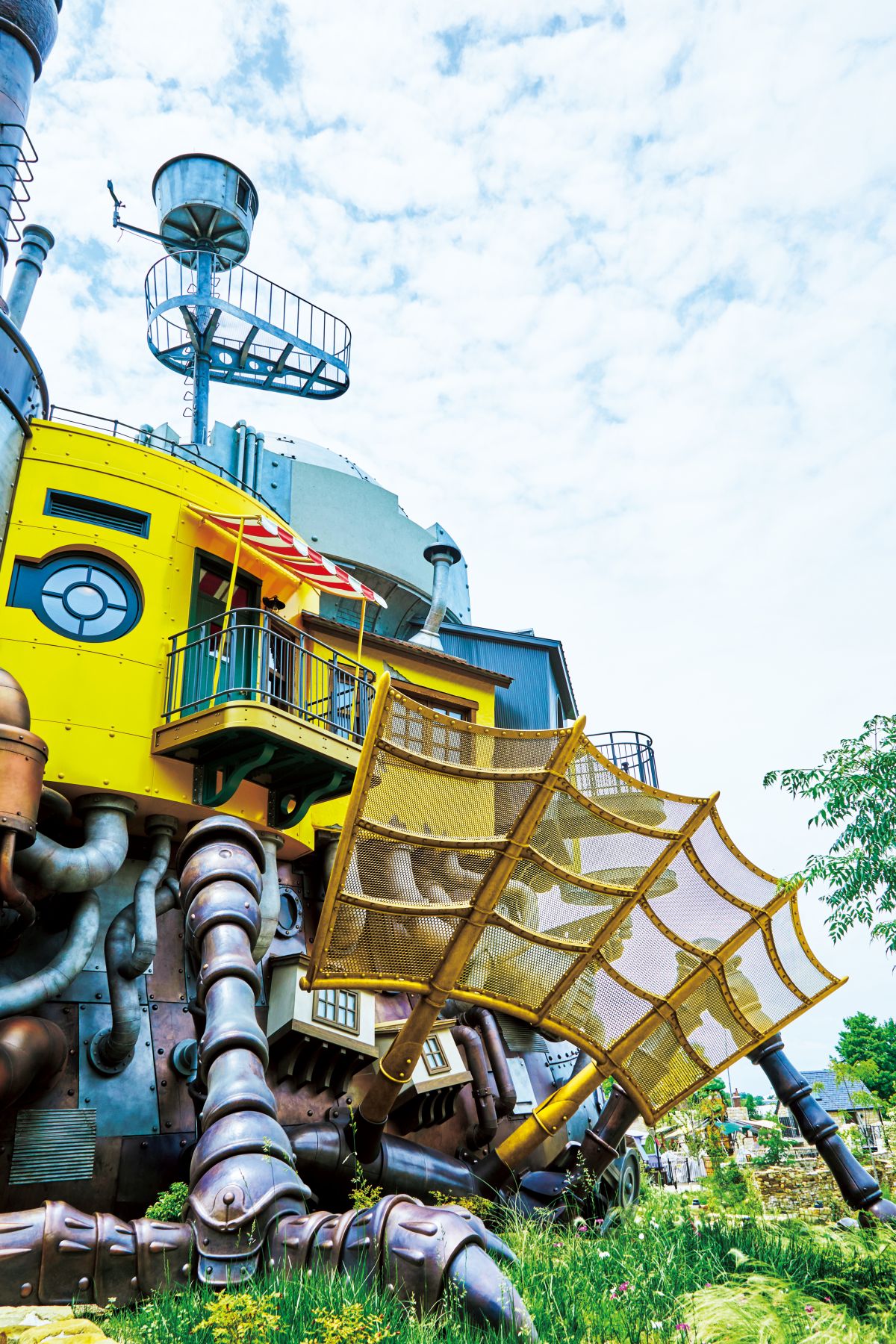
To achieve realism, the torso and legs of Howl's Castle are mostly covered with copper plates. However, copper is not a suitable material for outer panels with complex shapes. Therefore, Fujinuma devised a unique construction method.
"Copper plates are soft, so they can't hold the shape of the fuselage panels. So we put FRP on the base and then cover it with copper plates to keep the shape."
When Fujii heard the idea, he initially wondered whether it would work.
"But in reality, that was the only way we could do it. If we just bent the copper sheet, we wouldn't have been able to achieve the three-dimensional effect we had imagined. We were able to achieve that sense of volume precisely because we were creating the shape using the FRP base."
The copper plates used for the fuselage panels are 1mm thick. The legs are made from 2mm thick copper plates hammered into a wooden mold and attached directly to the frame without the use of FRP. While the attachment requires precision, the image of Howl's castle, with its "hodgepodge" and "wobbly" feel, was also created on-site. Fujinuma says:
"The locations where there would be gaps between panels or steps were also determined in the design drawings. For example, there would be four levels of step between panels. However, while adhering to the design rules, we often made adjustments on-site to create a more rugged look."
The fuselage panels incorporate concept design that makes it look like thick copper plates are peeling off and floating in places. Although there were specifications in the blueprints, delicate adjustments were made on site to create a realistic look as if the thick copper plates had been melted, even though they were made from 1mm copper plates. Kawahara says that this was possible because the entire team shared the same worldview.
"Everyone understands the worldview of what is being created, and makes on-site decisions to steadily improve the quality. It may have been unexpected to see both the creative and production teams working on manufacturing from the same perspective."
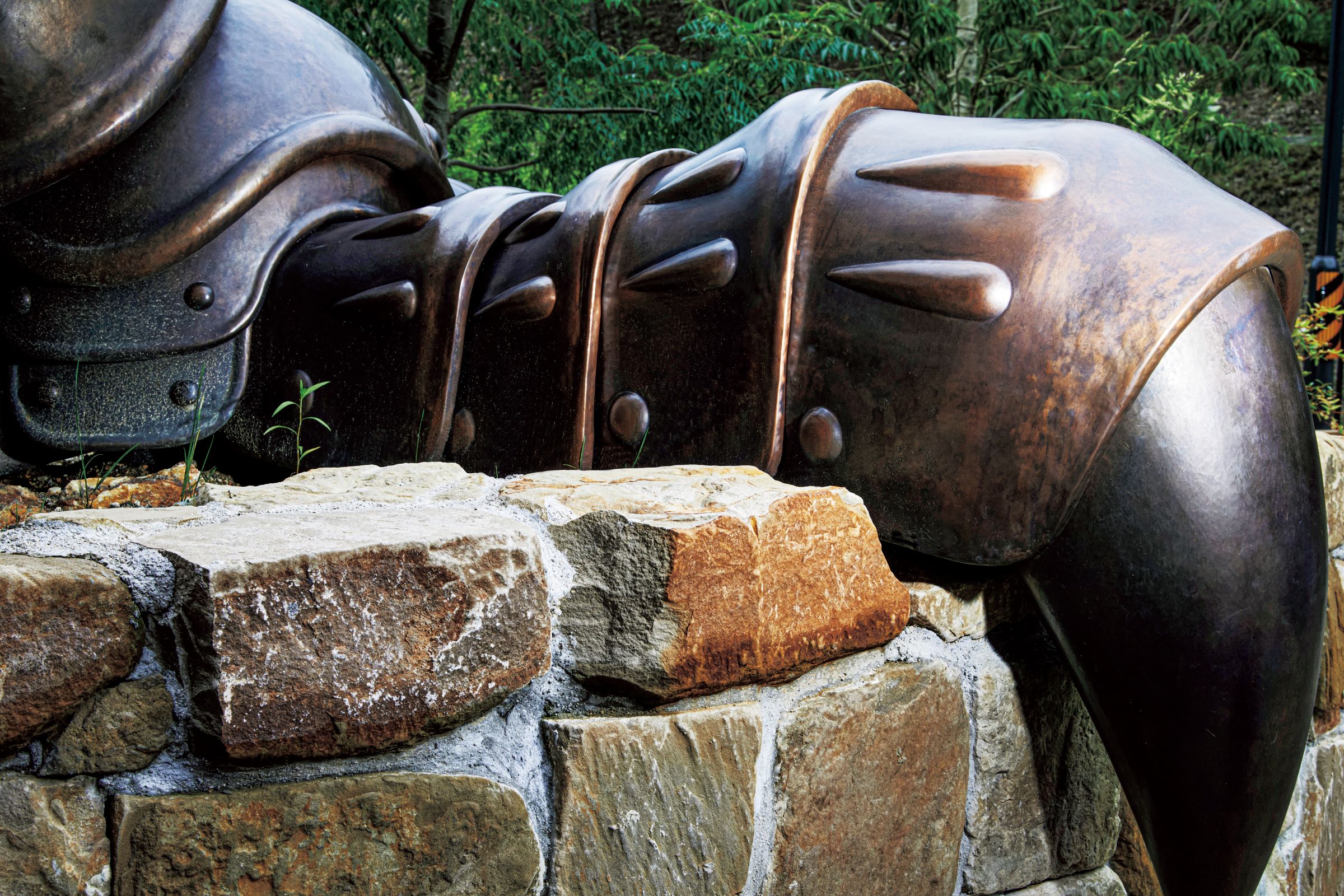
While the modeling panels were being installed, plans were also being made for how to present the exterior of the castle. Howl's castle is equipped with mechanisms that make it seem like a living thing, such as the rotation of the turrets, the up and down movement of cannons, the sounds that can be heard when entering the castle, and mist that erupts from several places on the outside. Kawahara says that these were also created while discussing the worldview with Director Goro.
"Director Goro told me that he wanted the movements to be quiet, not flashy, but in a way that suited the character's appearance, but expressing that was surprisingly difficult.
For example, when rotating a cannon, we didn't want it to move smoothly, but rather wanted it to move with a jerky motion to match the worldview of the castle. We used a mechanism for the rotation that was used for turntables in multi-storey car parks, but since it is originally designed to move smoothly, we controlled the movement with computer control to deliberately give it a jerky motion.
Even in terms of how the sound was created, initially it was influenced by the image of the monster-like castle at the beginning of the film, but after listening to it, Director Goro said, "It's a bit scary. I want something lighter, funnier, more comedic," and asked for revisions, so we remade it from scratch. In the end, we even sampled the sound of Calcifer, the fire demon, trying his best to move the castle but running out of strength, muttering, "This isn't good," and the sound of Director Goro whistling a bottle to create the sound."
The opposite value of overseas theme parks
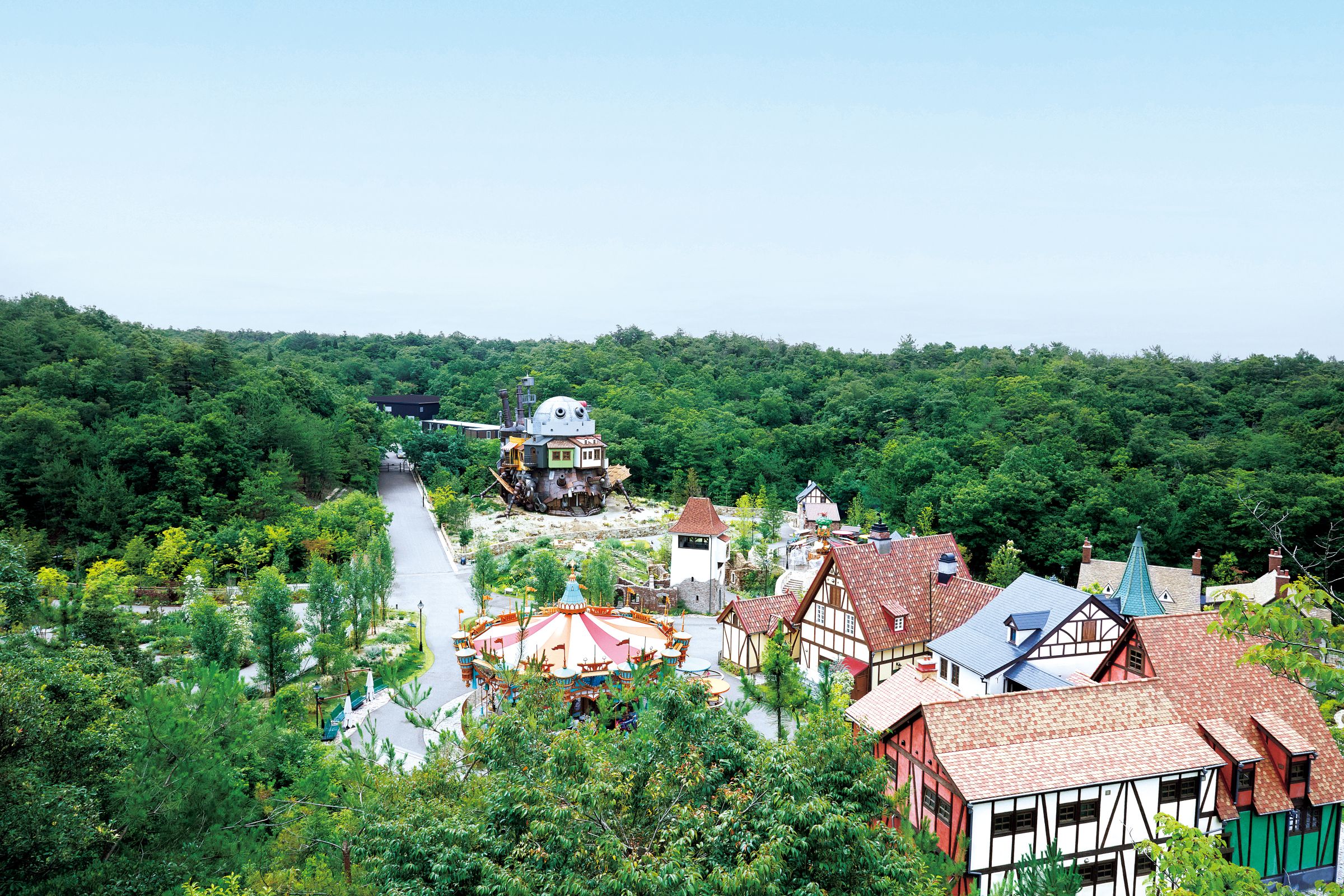
Thus, Howl's Castle was completed. When it opened, the staff and their families visited Ghibli Park.
"When I brought my kids here, they were amazed by the scale and the detail." (Fujinuma)
"I came with my parents and my wife, and my father said he was glad he could be involved in something that would leave a lasting legacy." (Murata)
"My daughter came dressed like Sophie and was really happy," said Kawahara.
The couple shared their feelings of being able to bring the world of the story to life together. Kawai, the sales representative, said she was in tears the moment the gates slid open on the morning of the opening day of Witch's Valley.
"I was put in charge of Ghibli Park immediately after joining the company, and it's been five years since then. When it was finally completed, I was incredibly moved to see visitors entering the park. Creating places that people can enjoy and that will remain in their memories is very rewarding, and I feel very happy to be able to do that."
Ghibli Park, including Howl's Castle, is often visited by people from overseas theme parks. Kawahara, who often attends these visitors, says that most of them show reactions of surprise and confusion.
"My impression is that the entire park has an approach that is the polar opposite of that of a typical theme park. There is too much information to organize. At a normal theme park, visitors can only look at displays, but most of them cannot be touched. The materials used for the sculptures are mainly FRP, rather than real metal.
But at Ghibli Park, even the small items on the desks are real, so that visitors can touch them. Basically, it's the real thing - that's what's so great about this park. Visitors from overseas are inspired and shocked by the sheer power of the real thing and the craftsmanship. They create that kind of dense quality. I'm really glad that we were able to help with that."
(Interviewed in July 2024. Titles in the article are those at the time of the interview.)
Photos and illustrations © Studio Ghibli
*Ghibli Park requires a reservation for a specific date. Please see the official website for details.
https://ghibli-park.jp/
profile
NOMURA Co.,Ltd.
Creative Division Executive Creative DirectorMasaki Kawahara
NOMURA Co.,Ltd.
Content Integration Center Technical Direction Department Room 3 ChiefFujii Kiyoto
NOMURA Co.,Ltd.
Creative Headquarters, Design Management Department, Design Division 2, design administration Section, ChiefHora Ratul
NOMURA Co.,Ltd.
Sales Promotion Headquarters, Third Business Division, Product Direction 2nd Department, Section 2, ChiefMurata Riku
NOMURA Co.,Ltd.
Sales Promotion Headquarters, 4th Business Division, Product Direction Department 1, Section 2, ChiefYasuhiro Fujinuma
NOMURA Co.,Ltd.
Sales Promotion Headquarters, First Business Division, Sales Department 1, Section 1, ChiefYuna Kawai
NOMURA Co.,Ltd.
Sales Promotion Headquarters Chubu Branch Product Direction Department ChiefRyoji Sugiura
NOMURA's Media
- NOMURA Co.,Ltd.SCENES
Please contact us using the button below if you have an inquiry, want to request a quote or request documents.
We have created a separate “FAQ page” that lists the most common questions we are asked.
Please take a look at this page if you have a question.